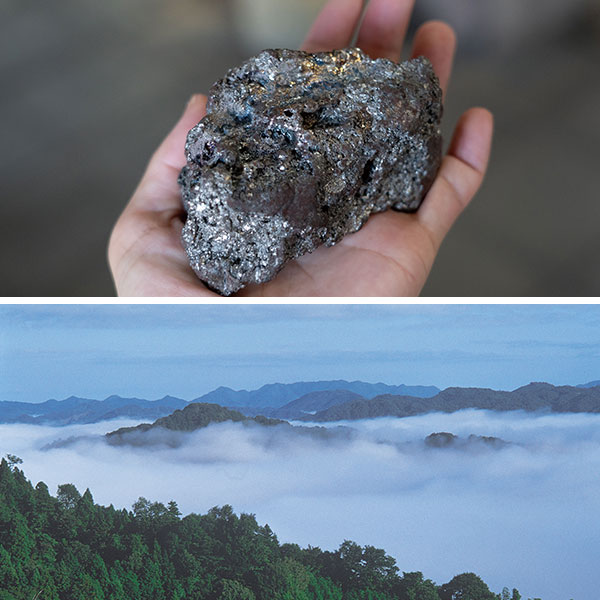
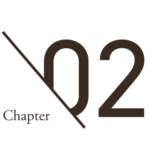
TRADITIONAL JAPANESE STEEL:
TAMAHAGANE
A UNIQUE JAPANESE STEEL ONLY PRODUCED IN SMALL QUANTITIES.
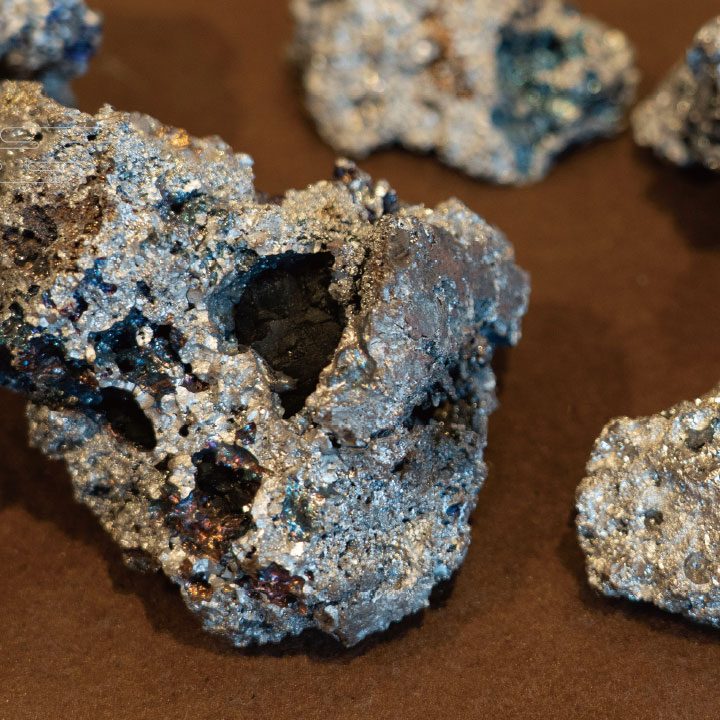
Tamahagane is produced using the traditional Tatara steel making method. It is a high-quality steel with very few impurities. It is very important in the production of Japanese swords that are required to, not bend, not break and cut well.
Many of the steel products we see on a daily basis are made from iron ore. In the early days of Japan, steel was manufactured using iron ore. However, since iron ore was scarce in Japan, tatara iron and steel production using iron sand as raw material began in the late 6th century. Through various improvements, Japan’s unique technology has been developed. With the modern tatara manufacturing method, it is possible to apply heat at high temperatures for long periods of time using a relatively small furnace and even by hand.
One cycle of the tatara method uses 10 tons of iron sand, and 12 tons of charcoal. However, this only produces around 900 kgs of tamahagane. It is extremely valuable. The steel made using the tatara method is extremely malleable. Then through the additional fold-forging process by the swordsmith, creates a level of uniformity to the steel’s internal crystalline structure. Thus, making the sword more resilient while at the same time creating the beautiful jihada patterns on the surface of the blade. It is the perfect raw material for making swords.
EASTERN SHIMANE, A LONG HISTORY OF TATARA STEEL PRODUCTION
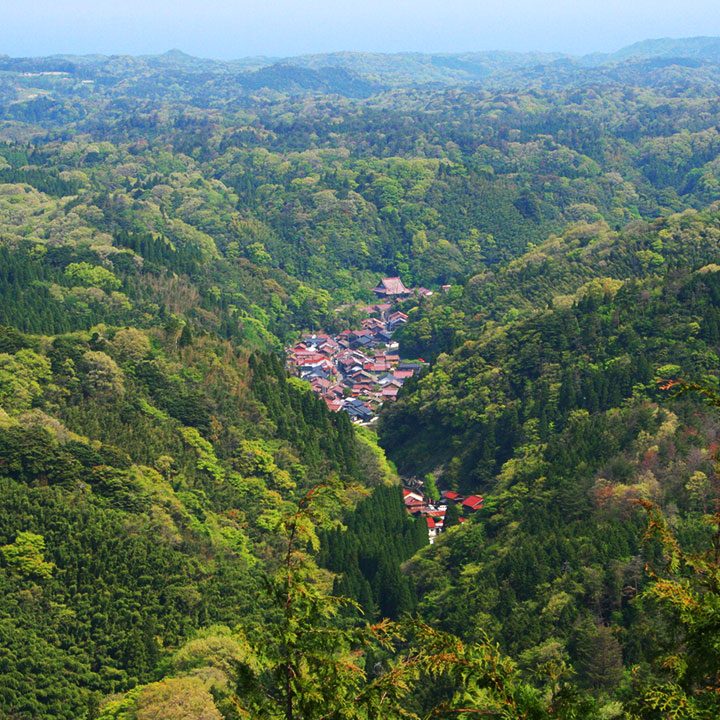
Due to the progression of technological improvements and an organized distribution system, at the peak of tatara iron production, more than 80% of the steel in Japan was made at the foot of the mountains of the Chugoku region. The geology of the Chugoku mountains contains copious amounts of high-quality iron-sand and is rich in forests that are necessary for charcoal production.
A group of artisans engaged in tatara iron manufacturing established a unique village-like society called, Sannai. The Sugaya Tatara Sannai in Unnan City is the only remaining historical facility in Japan where tatara iron and steel was actually made. It is a designated Important Cultural Property, and is open to the public. It is owned by the Tanabe family. The current head of the family, Tanabe Choemon (25th Generation), has recently restarted his family’s traditional tamahagane manufacturing business and built a new tatara furnace in Yoshida-cho, Unnan City.
There is a shrine in Yasugi City that is said to mark the spot where the god of iron-making, Kanayago, descended and pass on the knowledge of iron-making technology. It is still worshiped today by people involved in the iron making profession.
The NBTHK Tatara in Oku-Izumo also continues to manufacture tamahagane using the ancient Japanese tatara iron and steel making methods to supply swordsmith across Japan, and is recognized by the Japanese government as designated location for the preservation of traditional steel making techniques.
TATARA STEEL MANUFACTURE: A RELENTLESS 72 HOUR OPERATION
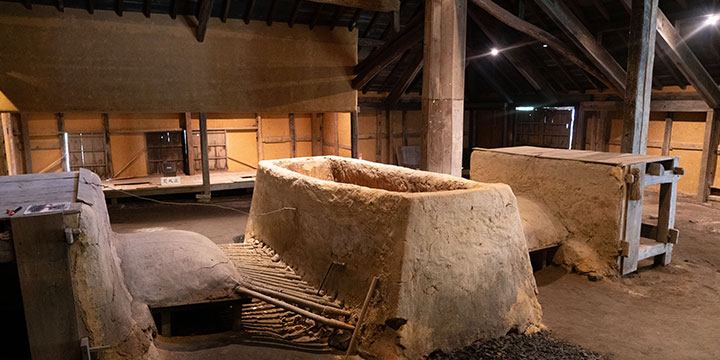
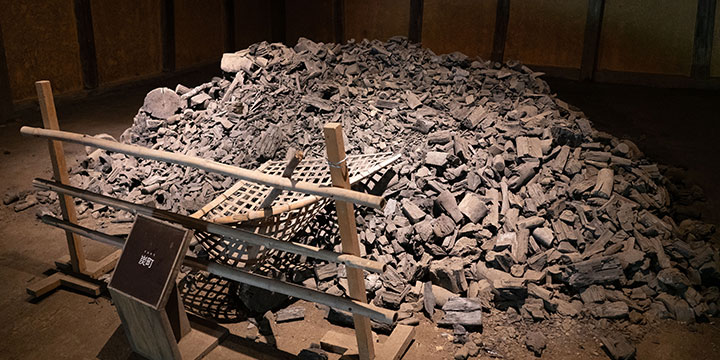
Tatara iron and steel making is a method in which iron is produced by burning iron sand and charcoal in a high-temperature clay furnace. A single cycle of a tatara iron manufacturing operation takes three days and three nights (72 hours). Each cycle is a one-time operation as it is necessary to destroy the furnace and remove the kera each time a cycle is completed. There is no room for error, as a failed kera cannot be rectified.
The Murage (foreman) checks on the condition of the bloom while it is forming at the bottom of the furnace via small holes in the walls. However, the internal condition of the kera cannot be seen from the outside, and it is not known if it is successful until the walls of the tatra have been broken down and the kera removed. Tatara Murage sharpen their senses to assess the situation inside the furnace by the sound and observing the flames. Then make adjustments to the amounts and places where the iron-sand is added.